螺杆与机筒的磨损及损伤分析
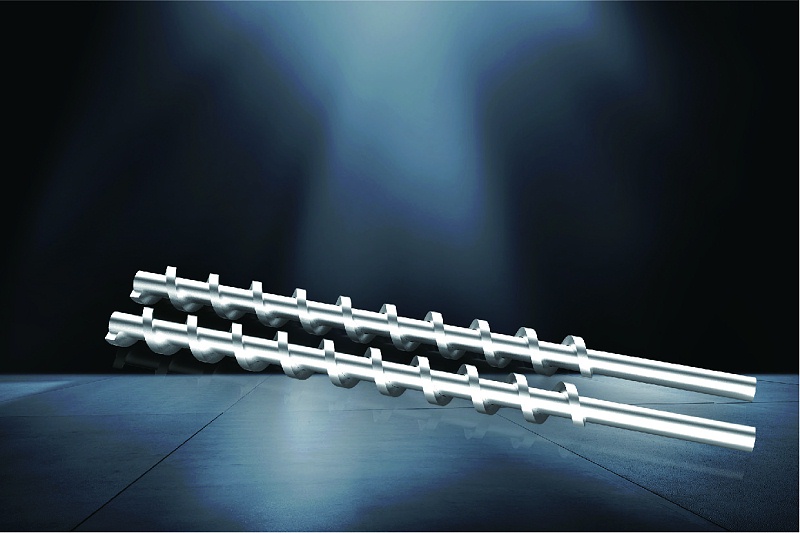
在螺杆挤出机的运作中,螺杆与
机筒的磨损主要集中在两个关键区域:加料区和计量区。不过在短时间内,这种磨损并不显著,可大致视为沿螺杆全长均匀分布。
加料区的磨损,主要是由于固体粒子与金属表面干摩擦引发的磨粒磨损。这一磨损区域相对较短,通常出现在固体粒料升温软化并开始熔融之前。
而计量区在液体摩擦环境下工作,面临的主要是腐蚀磨损风险。随着磨损加剧,螺杆与机筒之间的径向间隙会逐渐变大。严重时,漏流量大幅增加,挤出机的挤出效率会明显降低。相比之下,加料区的磨损对挤出量的影响并不突出。所以,在评估挤出系统的磨损状况时,通常以螺杆和机筒计量区部位的实测直径作为判断依据。
从理论和实际经验来看,当前国产单螺杆挤出机存在这样的情况:小直径螺杆制造时规定的径向间隙偏大,大直径螺杆的径向间隙则偏小。这就导致磨损变大的间隙,对小直径螺杆产量的影响更为明显。此外,大螺杆的制造成本较高,并且其磨损量一般也高于小直径螺杆。通常,我们会用径向间隙与螺杆计量段螺槽深度的比值,来确定螺杆的修复时机和使用周期。
对于小直径螺杆(直径60mm以下) ,当螺杆磨损后该比值达到初期的2 - 2.5倍时,若条件允许,就应考虑对螺杆进行修复或更换;当达到初期值的3倍时,则需要更换新螺杆。
实际上,螺杆的磨损并非局限于螺纹顶部。当挤出具有腐蚀性的物料时,螺槽底部和螺纹侧面所遭受的腐蚀磨损可能更为严重。螺纹磨损相对容易修复,而螺槽磨损由于区域较大,修复难度大大增加。所以,对于用于挤出腐蚀性物料的螺杆,在选择表面涂层材料及处理方法时,应将抗腐蚀性放在前边,抗磨损性次之。
除了正常磨损,螺杆和机筒还可能出现不正常损伤,常见于螺杆“环结”和异物“卡机”的情况。
螺杆环结,是指螺杆被凝结的物料紧紧抱死,无法转动。出现环结时,局部凝结的物料就像刹车闸瓦一样,死死刹住螺杆。如果双螺杆挤出机的驱动系统缺乏有效的保护装置,较大的驱动力很可能会扭断螺杆。环结现象主要发生在高熔点物料的挤出过程中。当螺杆熔融区的加热器失控,局部温度低于物料熔点时,已熔融的物料粘度会急剧增加,甚至重新凝结,或者固体粒子表面相互粘连,从而导致螺杆处于刹车状态。而对于低熔点物料,由于能够较容易地保持温度在熔点之上,所以很少出现环结现象。为预防环结发生,在开机前需要仔细检查加热器及温度控制仪表,确保其正常工作。在挤出作业过程中,也应定时检查仪表,实时监测各加热区的温度,一旦发现异常,立即处理。若螺杆发生环结,需立即停机,查找原因。在确认并修复加热系统故障点后,升高环结发生区及其相邻区域的温度,使环结物料充分熔融。手动盘车确认故障排除后,重新调整温度,恢复正常挤出工作。
螺杆的“卡机”,主要是因为金属等硬质异物混入原料,进入挤出系统后,与螺杆和机筒表面产生剧烈摩擦和挤轧,形成很大的阻力。此时,螺杆的动力消耗大幅增加,可能导致螺杆螺纹局部断裂、机筒被划伤,甚至螺杆被扭断。机筒一旦划伤,修复难度很大。螺杆螺纹局部断裂可通过堆焊的方式修复。为避免螺杆被物料中的硬质异物损伤,需要严格规范混料和加料操作。部分挤出机会在物料加入口处设置磁性或其他金属检测装置,当物料中混入金属异物时能及时警示,但对于陶瓷、玻璃、砂粒等非金属异物则无法检测。
在螺杆挤出机的设计中,通常会采取一系列保护措施。当出现环结或异物卡机情况时,能够使驱动源停止工作或与螺杆脱离,比如驱动电动机的电源保护和超载热继电器保护、三角皮带超载打滑以及专门设计的超载离合器等。